How augmented reality projection relieves the burden on measurement technicians in steel construction
In steel construction, measurement technicians often must contend with a high expenditure of time and resources. A particular difficulty is comparing the actual and target state of parts or assemblies and attachments after welding processes. This is the only way to derive or visualize the corresponding work instructions and specifications for the workers. However, measurement technicians can simplify and accelerate this complex process considerably using intelligent laser projection. This saves time and money, increases accuracy and enables the company to assert itself as an attractive partner on the market.
Measurement technicians in steel construction are often confronted with complex designs and special challenges, such as heat distortion during welding, which prolongs the production process. Complex tolerance management must be implemented (according to the Geometrical Product Specifications of ISO/TC 213 or ASME Y14.5). For example, higher tolerances are accepted for some parts or assemblies than for other, particularly critical parts that must be manufactured more precisely.
First, the measurement technicians must determine the exact actual state of the base body of the part or assembly and compare it with the target or planned state in order to be able to carry out any necessary rework on it immediately. In the following process stages, the other add-on parts must be adapted from the target state to the actual construction state in such a way that the required manufacturing tolerances are maintained. The aim is to avoid expensive and laborious rework in downstream process steps and to implement necessary adjustments – such as straightening parts or assemblies deformed by welding distortion, welding on additional material or removing material through grinding/milling processes – effectively in the process.
This complex process takes a lot of time. In addition, all other work on the part or assembly usually has to be interrupted for the measurement process so that the manual measurement can be carried out without interruption. Augmented reality projection (AR projection) is used to simplify, accelerate and make the process more precise.
The benefits of AR projection from EXTEND3D- Part of Atlas Copco Group
The dynamic laser projection reduces the manual effort in the production process by up to 75 percent. It can display the target position of the attachment on the weld body based on the measurement data from the measurement software, without the measurement technician having to mark its target coordinates manually. In this way, the solution from EXTEN3D – Part of Atlas Copco Group can significantly simplify the measurement process and accelerate the entire production of complex steel structures. With the improved process, companies gain an important competitive advantage. This is because the company can implement several orders in the same time. In addition, with the new solution, measurement technicians can use their employees for more demanding tasks and relieve them of tedious routine work. This helps to alleviate the shortage of skilled workers, increase the attractiveness of the workplace and attract young talent.
In steel construction projects, measurement technicians and workers work closely together. Depending on requirements, tactile measurement methods, such as a stencil, or optical methods, such as photogrammetry or laser trackers, are used to determine the current state of the basic structure of the steel construction. AR projection can be easily combined with all three methods. Tactile methods are particularly suitable for measuring high-precision parts or assemblies, while optical methods enable contactless, full-surface recording of the object surface. The laser tracker is ideal for objects with a very large surface, such as aircraft fuselage barrels or reactor chambers.
What requirements must be met?
Technically, the AR solution consists of a laser projector, two cameras and intelligent software to control the projector. To correctly visualize work steps, the software requires the coordinates of the measuring marks and the target coordinates of the attachments. These can be imported into the projection solution via a generic exchange interface. The projection solution from EXTEND3D – Part of Atlas Copco Group is able to easily read CSV files, the G3D format and all common CAD formats. The AR solution uses the cameras to recognize the markings on the part or assembly. Three to four such reference points in the field of view of the solution are necessary to orient oneself in space. This marker density is not a problem, as the markers were already needed for the previous measurement by the measurement technicians and can be reused.
Conclusion: The starting point for Industry 5.0
By using AR projection, measurement technicians can complete projects faster, more accurately and more cost-effectively. The assistance technology makes it possible to digitally optimize processes that are difficult to automate and to create an ideal interaction between technical support and human experience. AR projection thus paves the way for Industry 5.0 – the next stage of development in industry worldwide.
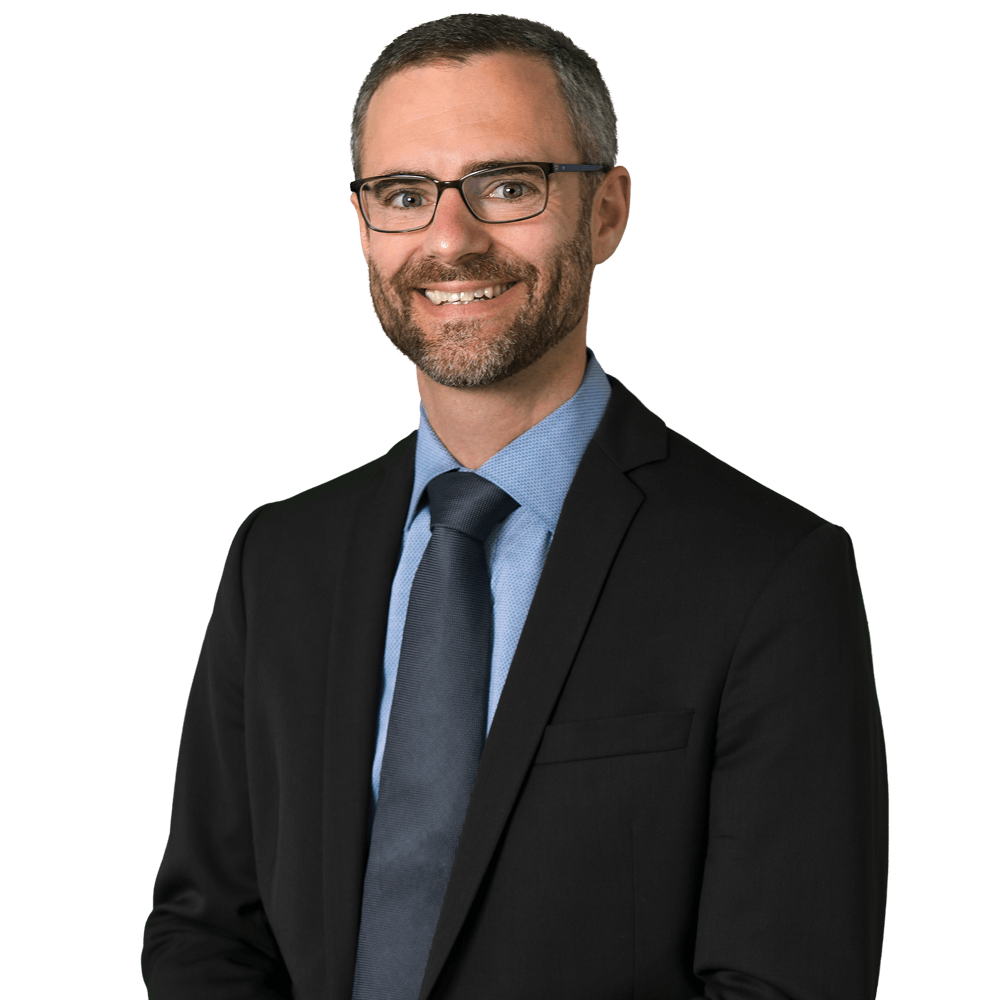